How Diesel Fuel Injection Systems Work
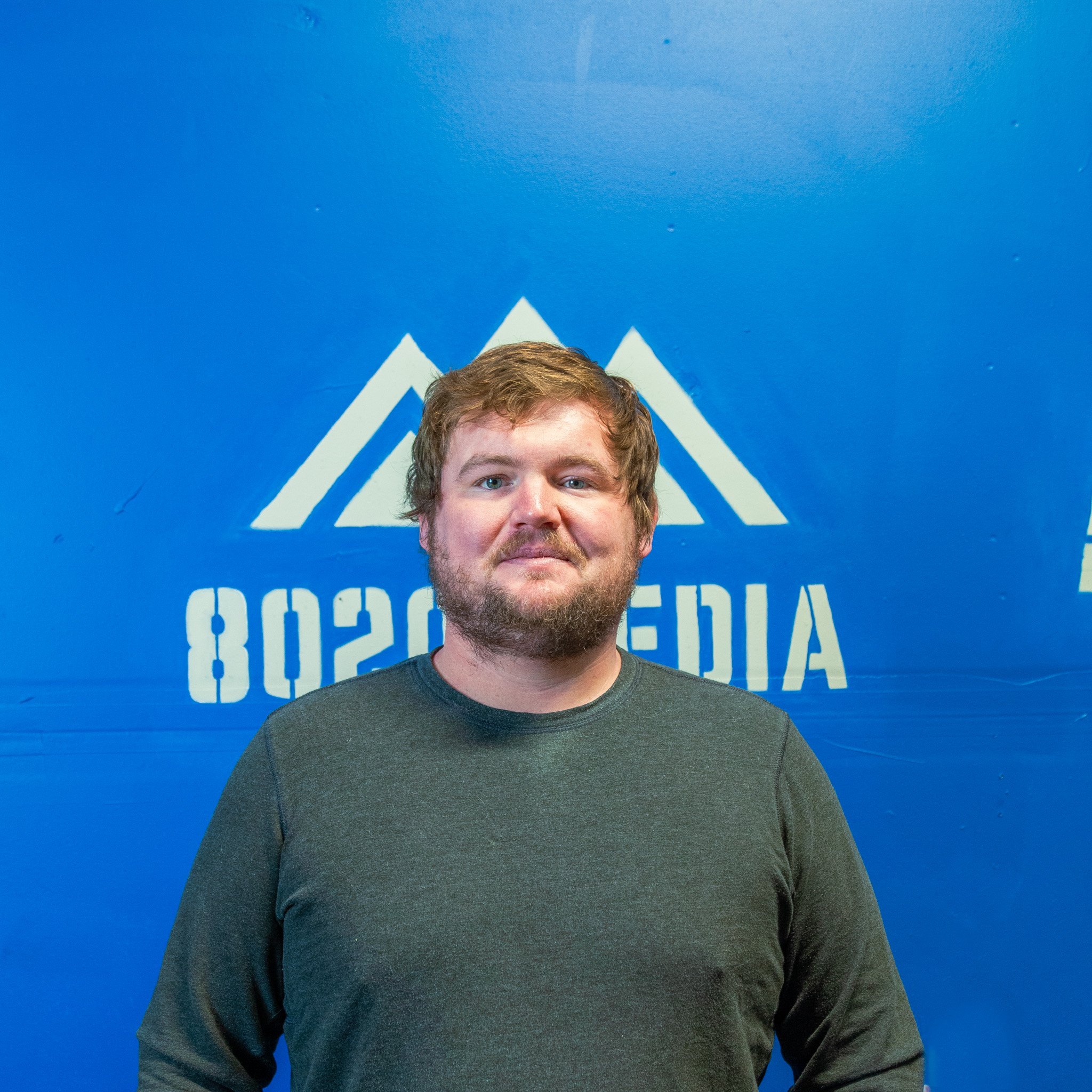
Meet Zach
Zach is one of the founders of 8020 Media and a lead writer for DieselIQ. He’s been in the automotive industry for over a decade and has published more than 400 articles for DieselIQ, TuningPro, BMWTuning, & more. His blend of automotive knowledge, writing & research skills, and passion make him an excellent resource for fellow diesel owners. His expertise goes beyond writing and includes a deep knowledge of Cummins and Powerstroke engines, as well as nearly 10 years of DIY experience. Zach is also experienced with tuning and has a wealth of technical knowledge that he brings to every article he writes.
The diesel fuel injection system is a major component of a properly operating engine. An engine out of adjustment can cause excessive exhaust smoke, poor fuel economy, heavy carbon buildup within the combustion chambers, and short engine life.
The diesel engine is known as a CI (compression ignition) engine, while the gasoline engine is known as a spark ignition engine.
Like the gasoline engine, the diesel engine is an internal combustion engine using either a two or four-stroke cycle. Combustion of fuel within the engine cylinders is the source of its power.
One difference in a diesel engine is diesel engines compress only the air within the combustion chamber. Another difference is, the speed of a diesel engine is controlled by the amount of fuel injected into the cylinders. In a gasoline engine, the speed of the engine is primarily controlled by the amount of air admitted into the carburetor or fuel injection system.
Diesel fuel is injected into the cylinder by a fuel injection system, which basically consists of a pump, fuel line, and injector or nozzle.
Compression Ratios & Fuel Injection
Compression ratios in diesel engines can be up to 24:1. This high compression ratio causes increased cylinder pressures of 400 to 600 psi, this in turn increases the air temperature inside the cylinder to such a high degree that it ignites the atomized diesel fuel that is injected.
Mechanically, the diesel engine is similar to the gasoline engine. The intake, compression, power, and exhaust strokes occur in the same order. The arrangement of the pistons, connecting rods, crankshaft, and engine valves is about the same. Diesel engines are also classified as in-line or v-type.
In comparison to the gasoline engine, the diesel engine is more efficient, produces more power per pound of fuel, is more reliable, is more durable because of the heavier construction needed for its high compression pressure, has lower fuel consumption for a given horsepower per hour, and presents less of a fire hazard.
These advantages are partially offset by higher initial cost and the greater requirements for starting due to the high compression pressure.
Diesel Fuel
Diesel fuel is heavier than gasoline because it is obtained from the residue of the crude oil after the more volatile fuels have been removed. As with gasoline, the efficiency of diesel fuel varies with the type of engine in which it is used. By distillation, cracking, and blending of several oils, a suitable diesel fuel can be obtained for all engine operating conditions. Using a poor or improper grade of fuel can cause hard starting, incomplete combustion, a smoky exhaust, and engine knocks.
The high injection pressures needed in the diesel fuel system are attained with close tolerances in the pumps and injectors. These tolerances make it necessary for the diesel fuel to have sufficient lubrication qualities to prevent rapid wear or damage. It must also be clean, mix rapidly with the air, and burn smoothly to produce an even thrust on the piston during combustion.
Diesel Engine Combustion Chamber Design
The fuel injected into the combustion chamber must be mixed thoroughly with the compressed air and distributed as evenly as possible throughout the chamber if the engine is to function at maximum efficiency and exhibit optimum drivability. A well designed diesel engine uses a combustion chamber designed for the intended usage of the engine. The injectors used should complement the combustion chamber. The combustion chambers described in the following sections are the most common designs currently in use.
Direct Injection Combustion Chamber
Direct injection is the most common combustion chamber and is now found in nearly all diesel engines. The fuel is injected directly into an open combustion chamber formed by the piston and cylinder head. The main advantage of this type of injection is that it is simple and has high fuel efficiency.
In the direct combustion chamber, the fuel must be atomized, vaporize and mix with the combustion air in a very short period of time. The shape of the piston helps with this during the intake stroke. Direct injection systems operate at very high pressures of up to 30,000 psi.
Indirect Injection Combustion Chamber
Indirect injection chambers were previously used mostly in passenger cars and light truck applications because of lower exhaust emissions and quietness. In today’s technology with electronic timing, direct injection systems are superior. Therefore, you will not see many indirect injections system on new engines; they are still on many older engines, however.
Pre-combustion Chamber
The pre-combustion chamber design used on indirect combustion diesel engines involves a separate combustion chamber located in either the cylinder head or wall. This pre-combustion chamber takes up from 20% – 40% of the combustion chambers TDC volume and is connected to the chamber by one or more passages. As the compression stroke occurs, the air is forced up into the precombustion chamber. When fuel is injected into the precombustion chamber, it partially burns, building up pressure. This pressure forces the mixture back into the combustion chamber, and complete combustion occurs.
Methods of Diesel Fuel Injection
You may have heard the statement, “The fuel injection system is the actual heart of the diesel engine.” When you consider that indeed a diesel could not be developed until an adequate fuel injection system was designed and produced, this statement takes on a much broader and stronger meaning.
There have been many important developments in pumps, nozzles, and unit injectors for diesel engines over the years, with the latest injection system today relying on electronic controls and sensors.
Diesel Fuel Injection Systems
Diesel fuel injection systems must accomplish five particular functions: meter, inject, time, atomize, and create pressure.
1. Metering
Accurate metering or measuring of the fuel means, that for the same fuel control setting, the same quantity of fuel must be delivered to each cylinder for each power stroke of the engine. Only in this way can the engine operate at a uniform speed with uniform power output.
Smooth engine operation and an even distribution of the load between the cylinders depend upon the same volume of fuel being admitted to a particular cylinder each time it fires and upon equal volumes of fuel being delivered to all cylinders of the engine.
2. Injection control
A fuel system must also control the rate of injection. The rate at which fuel is injected determines the rate of combustion. The rate of injection at the start should be low enough that excessive fuel does not accumulate in the cylinder during the initial ignition delay (before combustion begins). Injection should proceed at such a rate that the rise in combustion pressure is not too great, yet the rate of injection must be such that fuel is introduced as rapidly as possible to obtain complete combustion.
An incorrect rate of injection affects engine operation in the same way as improper timing. When the rate of injection is too high, the results are similar to those caused by an injection that is too early; when the rate is too low, the results are similar to those caused by an injection that is too late.
3. Timing
In addition to measuring the amount of fuel injected, the system must properly time injection to ensure efficient combustion so that maximum energy can be obtained from the fuel. When the fuel is injected too early in the cycle, ignition may be delayed because the temperature of the air at this point is not high enough. An excessive delay, on the other hand, gives rough and noisy operation of the engine. It also permits some fuel to be lost due to the wetting of the cylinder walls and piston head.
This in turn results in poor fuel economy, high exhaust gas temperature, and smoke in the exhaust. When fuel is injected too late in the cycle, all the fuel will not be burned until the piston has traveled well past top center. When this happens, the engine does not develop enough power, the exhaust is smoky, and fuel consumption is high.
4. Atomization of fuel
As used in connection with fuel injection, atomization means the breaking up of the fuel as it enters the cylinder into small particles which form a mist-like spray. Atomization of the fuel must meet the requirements of the type of combustion chamber in use. Some chambers require very fine atomization, while others function with dispersed atomization. Proper atomization makes it easier to start the burning process and ensures that each minute particle of fuel is surrounded by particles of oxygen that it can combine with.
Atomization is generally obtained when liquid fuel, under high pressure, passes through the small opening (or openings) in the injector or nozzle. As the fuel enters the combustion space, high velocity is developed because the pressure in the cylinder is lower than the fuel pressure. The created friction, resulting from the fuel passing through the air at high velocity, causes the fuel to break up into small particles.
5. Creating pressure
A fuel injection system must increase the pressure of the fuel to overcome compression pressure and to ensure proper dispersion of the fuel injected into the combustion space. Proper dispersion is essential if the fuel is to mix thoroughly with the air and burn efficiently. While pressure is a chief contributing factor, the dispersion of the fuel is influenced, in part, by atomization and penetration of the fuel. (Penetration is the distance through which the fuel particles are carried by the motion given them as they leave the injector or nozzle.)
If the atomization process reduces the size of the fuel particles too much, they will lack penetration. Too little penetration results in the small particles of fuel igniting before they have been properly distributed or dispersed in the combustion space. Since penetration and atomization tend to oppose each other, a compromise in the degree of each is necessary in the design of the fuel injection equipment, particularly if uniform distribution of fuel within the combustion chamber is to be obtained.
Types of Diesel Fuel Injection Systems
Diesel engines are equipped with one of several distinct types of fuel injection systems: individual pump system; multiple-plunger, inline pump system; unit injector system; pressure-time injection system; distributor pump system; and common rail injection system.
Common Rail Injection Pump System
The common rail injection is the newest high-pressure direct injection fuel delivery system. An advanced design fuel pump supplies fuel to a common rail that acts as a pressure accumulator. The common rail delivers fuel to the individual injectors via short high-pressure fuel lines. The system’s electronic control unit precisely controls both the rail pressure and the timing and duration of the fuel injection. Injector nozzles are operated by rapid-fire solenoid valves or piezo-electric triggered actuators.
Hydraulic Electronic Unit Injector (HEUI)
The hydraulic electronic unit injectors use high pressure engine oil to provide the force needed to complete injection. Many of the mechanical drive components found in standard mechanical or electronic unit injection systems are not used in this system.
A solenoid on each injector controls the amount of fuel delivered by the injector. A gear driven axial pump raises the normal pressure to the levels required by the injectors. The ECM sends a signal to an injection pressure control valve to control pressure, and another signal to each injector solenoid to inject the fuel.
Pressure in the engine oil manifold is controlled by the ECM through the use of an injection pressure control valve. The injection pressure control valve, or dump valve, controls the injection pump outlet pressure by dumping excess oil back to the sump. The ECM monitors pressure in the manifold through an injection control pressure (ICP) sensor. The ECM measures the pressure sensor signal to the desired injection pressure. Based on this measurement, the ECM changes the oil pressure in the high pressure manifold.
High pressure oil is routed from the pump to the high pressure manifold through a steel tube. From there it is routed to each injector through shorter jumper tubes.
Thank you, and this article is very informative. Except that I am experiencing a fuel leak in the valley on the fuel rail between low pressure fuel pump and fuel inlet tubes to the injector rails. I have located the fuel leak squirting out from a component, I guess a pressure accumulator, I’m not sure the correct name.
Is it possible for you to please forward me the correct name so that I could order the correct part , the vehicle is a 97’Ford E-350, 7.3L , V8 powerstroke diesel.
Your engine uses the HEUI system and not common rail. Are you aware of that?
Wait, 97? That indirect injection?